Laser Cut Fire Proximity Suit
Why Use Laser to Cut Fire Proximity Suit?
Laser cutting is the preferred method for manufacturing Fire Proximity Suits due to its precision, efficiency, and ability to handle advanced Fire Proximity Suit materials like aluminized fabrics, Nomex®, and Kevlar®.
Speed & Consistency
Faster than die-cutting or knives, especially for custom/low-volume production.
Ensures uniform quality across all suits.
Sealed Edges = Enhanced Safety
Laser heat naturally bonds synthetic fibers, reducing loose threads that could ignite near flames.
Flexibility for Complex Designs
Easily adapts to cutting reflective coatings, moisture barriers, and thermal linings in one pass.
Precision & Clean Edges
Lasers produce razor-sharp, sealed cuts, preventing fraying in heat-resistant layers.
Ideal for intricate designs (e.g., seams, vents) without damaging sensitive materials.
No Physical Contact
Avoids distortion or delamination of multi-layer Fire Proximity Suit material, preserving insulation properties.
What fabrics can be used to make firefighting suits?
Firefighting suits can be made from the following fabrics
Aramid – e.g., Nomex and Kevlar, heat-resistant and flame-retardant.
PBI (Polybenzimidazole Fiber) – Extremely high heat and flame resistance.
PANOX (Pre-oxidized Polyacrylonitrile Fiber) – Heat-resistant and chemical-proof.
Flame-Retardant Cotton – Chemically treated to enhance fire resistance.
Composite Fabrics – Multi-layered for thermal insulation, waterproofing, and breathability.
These materials protect firefighters from high temperatures, flames, and chemical hazards.
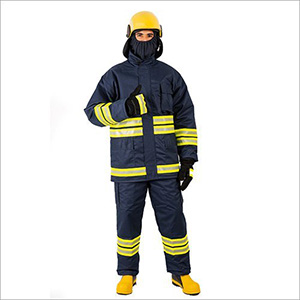
Laser tutorial 101
Guide to the Best Laser Power for Cutting Fabrics
video description:
In this video, we can see that different laser cutting fabrics require different laser cutting powers and learn how to choose laser power for your material to achieve clean cuts and avoid scorch marks.
Advantages of Laser Cut Fire Proximity Suit
✓ Precision Cutting
Delivers clean, sealed edges on Fire Proximity Suit materials (Nomex®, Kevlar®, aluminized fabrics), preventing fraying and maintaining structural integrity.
✓ Enhanced Safety Performance
Laser-fused edges reduce loose fibers, minimizing ignition risks in extreme heat environments.
✓ Multi-Layer Compatibility
Cuts through reflective outer layers, moisture barriers, and thermal linings in a single pass without delamination.
✓ Customization & Complex Designs
Enables intricate patterns for ergonomic mobility, strategic venting, and seamless seam integration.
✓ Consistency & Efficiency
Ensures uniform quality across mass production while reducing material waste compared to die-cutting.
✓ No Mechanical Stress
Contactless process avoids fabric distortion, critical for maintaining the Fire Proximity Suit’s thermal protection.
✓ Regulatory Compliance
Meets NFPA/EN standards by preserving material properties (e.g., heat resistance, reflectivity) post-cutting.
Fire Proximity Suit Laser Cut Machine Recommend
• Working Area: 1600mm * 1000mm (62.9” * 39.3 ”)
• Laser Power: 100W/150W/300W
• Working Area: 1600mm * 3000mm (62.9’’ *118’’)
• Laser Power: 150W/300W/500W
Intro. of Main Cloth for Fire Proximity Suits
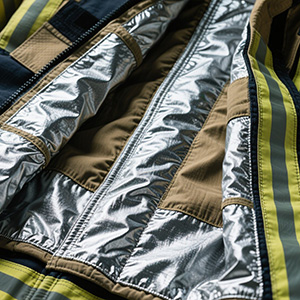
Fire Suit Three Layer Structure
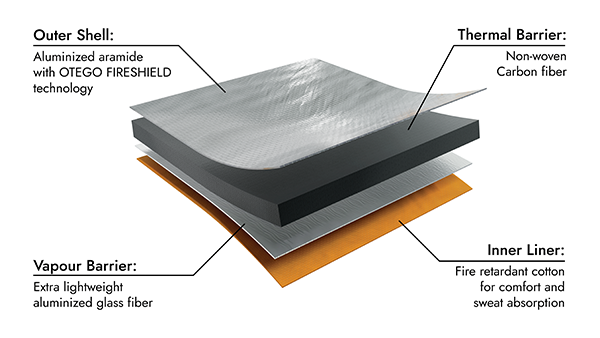
Structure Of Fire Suit
Fire proximity suits rely on advanced multi-layer fabric systems to protect against extreme heat, flames, and thermal radiation. Below is an in-depth breakdown of the primary materials used in their construction.
Aluminized Fabrics
Composition: Fiberglass or aramid fibers (e.g., Nomex/Kevlar) coated with aluminum.
Advantages: Reflects >90% of radiant heat, withstands brief exposure to 1000°C+.
Applications: Wildland firefighting, foundry work, industrial furnace operations.
Nomex® IIIA
Properties: Meta-aramid fiber with inherent flame resistance (self-extinguishing).
Advantages: Excellent thermal stability, arc flash protection, and abrasion resistance.
PBI (Polybenzimidazole)
Performance: Exceptional heat resistance (up to 600°C continuous exposure), low thermal shrinkage.
Limitations: High cost; used in aerospace and elite firefighting gear.
Aerogel Insulation
Properties: Ultra-lightweight nanoporous silica, thermal conductivity as low as 0.015 W/m·K.
Advantages: Superior heat blockage without bulk; ideal for mobility-critical suits.
Carbonized Felt
Composition: Oxidized polyacrylonitrile (PAN) fibers.
Advantages: High-temperature resilience (800°C+), flexibility, and chemical resistance.
Multi-Layer FR Batting
Materials: Needle-punched Nomex® or Kevlar® felt.
Function: Traps air to enhance insulation while maintaining breathability.
Outer Shell (Thermal Reflective/Flame Barrier Layer)
FR Cotton
Treatment: Phosphorous or nitrogen-based flame-retardant finishes.
Advantages: Breathable, hypoallergenic, cost-effective.
Nomex® Delta T
Technology: Moisture-wicking blend with permanent FR properties.
Use Case: Prolonged wear in high-heat environments.
Function: Directly faces extreme heat, reflecting radiant energy and blocking flames.
Mid-Layer (Thermal Insulation)
Function: Blocks conductive heat transfer to prevent burns.
Inner Liner (Moisture Management & Comfort)
Function: Wicks sweat, minimizes heat stress, and improves wearability.