Laser Cutting Neoprene Fabric
Introduction
What is Neoprene Fabric?
Neoprene fabric is a synthetic rubber material made from polychloroprene foam, known for its exceptional insulation, flexibility, and water resistance. This versatile neoprene fabric material features a closed-cell structure that traps air for thermal protection, making it ideal for wetsuits, laptop sleeves, orthopedic supports, and fashion accessories. Resistant to oils, UV rays, and extreme temperatures, neoprene fabric maintains durability while providing cushioning and stretch, adapting seamlessly to both aquatic and industrial applications.
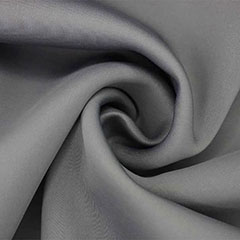
Neoprene Fabric
Neoprene Features
Thermal Insulation
Closed-cell foam structure traps air molecules
Maintains consistent temperature in wet/dry conditions
Critical for wetsuits (1-7mm thickness variants)
Elastic Recovery
300-400% elongation capacity
Returns to original shape after stretching
Superior to natural rubber in fatigue resistance
Chemical Resistance
Impervious to oils, solvents and mild acids
Withstands ozone and oxidation degradation
Operating range: -40°C to 120°C (-40°F to 250°F)
Buoyancy & Compression
Density range: 50-200kg/m³
Compression set <25% (ASTM D395 testing)
Progressive resistance to water pressure
Structural Integrity
Tensile strength: 10-25 MPa
Tear resistance: 20-50 kN/m
Abrasion-resistant surface options available
Manufacturing Versatility
Compatible with adhesives/laminates
Die-cuttable with clean edges
Customizable durometer (30-80 Shore A)
History and Innovations
Types
Standard Neoprene
Eco-Friendly Neoprene
Laminated Neoprene
Technical Grades
Specialty Types
Future Trends
Eco-materials - Plant-based/recycled options (Yulex/Econyl)
Smart features - Temperature-adjusting, self-repairing
Precision tech - AI-cut, ultra-light versions
Medical uses - Antibacterial, drug-delivery designs
Tech-fashion - Color-changing, NFT-linked wear
Extreme gear - Space suits, deep-sea versions
Historical Background
Developed in 1930 by DuPont scientists as the first synthetic rubber, originally called "DuPrene" (later renamed Neoprene).
Initially created to address natural rubber shortages, its oil/weather resistance made it revolutionary for industrial use.
Material Comparison
Property | Standard Neoprene | Eco Neoprene (Yulex) | SBR Blend | HNBR Grade |
---|---|---|---|---|
Base Material | Petroleum-based | Plant-based rubber | Styrene mix | Hydrogenated |
Flexibility | Good (300% stretch) | Excellent | Superior | Moderate |
Durability | 5-7 years | 4-6 years | 3-5 years | 8-10 years |
Temp Range | -40°C to 120°C | -30°C to 100°C | -50°C to 150°C | -60°C to 180°C |
Water Resist. | Excellent | Very Good | Good | Excellent |
Eco-Footprint | High | Low (biodegradable) | Medium | High |
Neoprene Applications
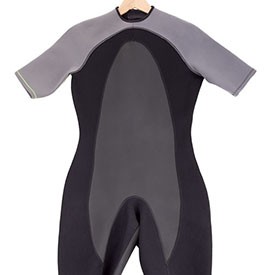
Water Sports & Diving
Wetsuits (3-5mm thick) – Traps body heat with closed-cell foam, ideal for surfing and diving in cold water.
Dive skins/swim caps – Ultra-thin (0.5-2mm) for flexibility and friction protection.
Kayak/SUP padding – Shock-absorbing and comfortable.
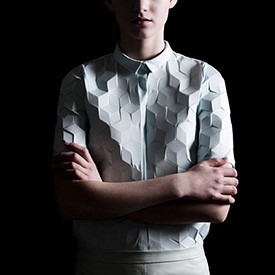
Fashion & Accessories
Techwear jackets – Matte finish + waterproof, popular in urban fashion.
Waterproof bags – Lightweight and wear-resistant (e.g., camera/laptop sleeves).
Sneaker liners – Enhances foot support and cushioning.
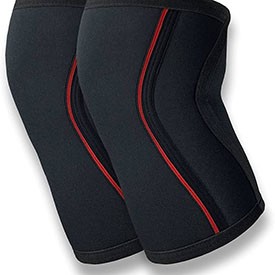
Medical & Orthopedic
Compression sleeves (knee/elbow) – Gradient pressure improves blood flow.
Post-surgery braces – Breathable & antibacterial options reduce skin irritation.
Prosthetic padding – High elasticity minimizes friction pain.
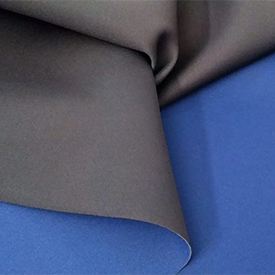
Industrial & Automotive
Gaskets/O-rings – Oil & chemical-resistant, used in engines.
Machine vibration dampers – Reduces noise and shock.
EV battery insulation – Flame-retardant versions improve safety.
How to Laser Cut Neoprene Fabric?
CO₂ lasers are ideal for burlap, offering a balance of speed and detail. They provide a natural edge finish with minimal fraying and sealed edges.
Their efficiency makes them suitable for large-scale projects like event decor, while their precision allows for intricate patterns even on the coarse texture of burlap.
Step-by-Step Process
1. Preparation:
Use fabric-faced neoprene (avoids melting issues)
Flatten before cutting
2. Settings:
CO₂ laser works best
Start with low power to prevent burning.
3. Cutting:
Ventilate well (cuts produce fumes)
Test settings on scrap first
4. Post-Processing:
Leaves smooth, sealed edges
No fraying - ready to use
Related Videos
Can You Laser Cut Nylon (Lightweight Fabric)?
In this video we used a piece of ripstop nylon fabric and one industrial fabric laser cutting machine 1630 to make the test. As you can see, the effect of laser cutting nylon is excellent.
Clean and smooth edge, delicate and precise cutting into various shapes and patterns, fast cutting speed and automatic production.
Can you Laser Cut Foam?
The short answer is yes - laser-cutting foam is absolutely possible and can produce incredible results. However, different types of foam will laser cut better than others.
In this video, explore whether laser cutting is a viable option for foam and compare it to other cutting methods like hot knives and waterjets.
Any Question to Laser Cutting Neoprene Fabric?
Let Us Know and Offer Further Advice and Solutions for You!
Recommended Neoprene Laser Cutting Machine
At MimoWork, we are laser cutting specialists dedicated to revolutionizing textile manufacturing through innovative Neoprene fabric solutions.
Our proprietary cutting-edge technology overcomes traditional production limitations, delivering precision-engineered results for international clients.
Laser Power: 100W/150W/300W
Working Area (W * L):1600mm * 1000mm (62.9” * 39.3 ”)
Laser Power: 100W/150W/300W
Working Area (W * L): 1800mm * 1000mm (70.9” * 39.3 ”)
Laser Power: 150W/300W/450W
Working Area (W * L): 1600mm * 3000mm (62.9’’ *118’’)
FAQs
Neoprene fabric is a synthetic rubber material known for its durability, flexibility, and resistance to water, heat, and chemicals. It was first developed by DuPont in the 1930s and is widely used in various industries due to its unique properties.
Yes, neoprene can be great for certain types of clothing, but its suitability depends on the design, purpose, and climate.
Neoprene fabric is durable, water-resistant, and insulating, making it great for wetsuits, fashion, and accessories. However, it has key drawbacks: poor breathability (traps heat and sweat), heftiness (stiff and bulky), limited stretch, difficult care (no high heat or harsh washing), potential skin irritation, and environmental concerns (petroleum-based, non-biodegradable). While ideal for structured or waterproof designs, it’s uncomfortable for hot weather, workouts, or long wear. Sustainable alternatives like Yulex or lighter fabrics like scuba knit may be better for certain uses.
Neoprene is expensive due to its complex petroleum-based production, specialized properties (water resistance, insulation, durability), and limited eco-friendly alternatives. High demand in niche markets (diving, medical, luxury fashion) and patented manufacturing processes further drive up costs, though its long lifespan can justify the investment. For cost-conscious buyers, alternatives like scuba knit or recycled neoprene may be preferable.
Neoprene is a high-quality material prized for its durability, water resistance, insulation, and versatility in demanding applications like wetsuits, medical braces, and high-fashion apparel. Its long lifespan and performance in harsh conditions justify its premium cost. However, its stiffness, lack of breathability, and environmental impact (unless using eco-friendly versions like Yulex) make it less ideal for casual wear. If you need specialized functionality, neoprene is an excellent choice—but for everyday comfort or sustainability, alternatives like scuba knit or recycled fabrics may be better.