Foam Cutting Machine: Why Choose Laser?
When it comes to foam cutting machine, cricut machine, knife cutter, or water jet are the first options poping into mind. But laser foam cutter, a new technology used in cutting insulation materials, are gradually becoming the main force in the market thanks to the high precision and high speed cutting advantages. If you are looking for a cutting machine for foam board, foam core, eva foam, foam mat, this article will be your helper for you to evaluate and choose suitable cutting foam machine.
Cricut Machine

Processing Method: Cricut machines are digital cutting tools that use blades to cut through foam based on computer-generated designs. They are versatile and can handle various foam types and thicknesses.
Advantages: Precise cutting of intricate designs, easy to use with pre-designed templates, suitable for small-scale foam cutting projects.
Limitations: Limited to certain foam thicknesses, may struggle with very dense or thick foam materials.
Knife Cutter
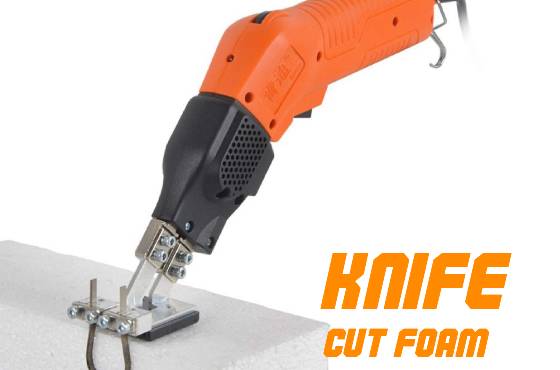
Processing Method: Knife cutters, also known as blade or oscillating cutters, use a sharp blade to cut through foam based on programmed patterns. They can cut straight lines, curves, and detailed shapes.
Advantages: Versatile for cutting different foam types and thicknesses, good for creating complex shapes and patterns.
Limitations: Limited to 2D cutting, may require multiple passes for thick foam, blade wear may affect cutting quality over time.
Water Jet
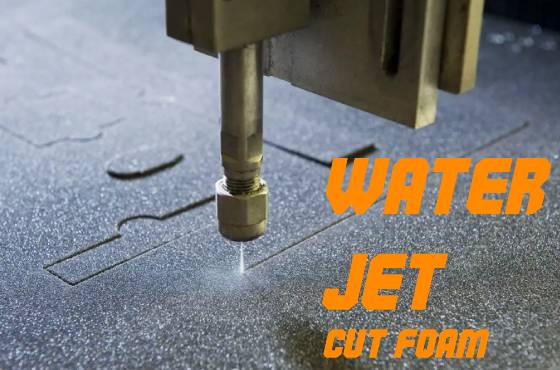
Processing Method: Water jet cutting uses a high-pressure stream of water mixed with abrasive particles to cut through foam. It is a versatile method that can cut through thick foam materials and produce clean edges.
Advantages: Can cut through thick and dense foam, produces clean and precise cuts, versatile for various foam types and thicknesses.
Limitations: Requires a water jet cutting machine and abrasive material, higher operating costs compared to other methods, may not be as precise as laser cutting for intricate designs.
Laser Cutter
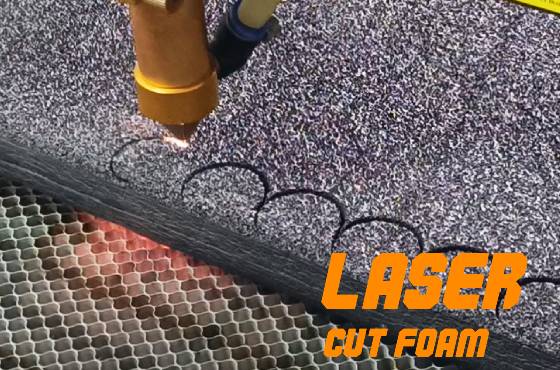
Processing Method: Laser cutting machines use a focused laser beam to cut through foam by vaporizing the material along a predetermined path. They offer high precision and can create intricate designs.
Advantages: Precise and detailed cutting, suitable for complex shapes and fine details, minimal material waste, versatile for various foam types and thicknesses.
Limitations: Initial setup and calibration required, higher initial cost compared to other methods, safety precautions needed due to laser use.
Comparison: which one is better to cut foam?
Talk about Precision:
Laser cutting machines offer the highest precision and detail for intricate designs, followed by water jet cutting, while Cricut machines and hot wire cutters are suitable for simpler cuts.
Talk about Versatility:
Laser cutting machines, water jet cutting, and hot wire cutters are more versatile for handling various foam types and thicknesses compared to Cricut machines.
Talk about Complexity:
Cricut machines are simpler to use with pre-designed templates, while hot wire cutters are suitable for basic shaping, laser cutting, and water jet cutting for more complex shapes and designs.
Talk about Cost:
Cricut machines are generally more affordable, while laser cutting machines and water jet cutting require higher initial investment and regular maintenance.
Talk about Safety:
Laser cutting machines, water jet cutting, and hot wire cutters require safety precautions due to heat, high-pressure water, or laser use, while Cricut machines are generally safer to operate.
In summary, if you have a long-term foam production plan, and would like more custom and characteristic products, to get more added value from that, a laser foam cutter will be your ideal choice. The foam laser cutter offers higher precision production while enhancing cutting efficiency. There are higher and consistent profits from laser cutting foam even if you need to invest in the machine in the early stage. Automatic processing is beneficial to expand production scale. For the other, if you have requirements for custom and flexible processing, the foam laser cutter is qualified for it.
▽
✦ High Cutting Precision
Thanks to the digital control system and fine laser beam, the foam laser cutters offer high precision and accuracy in cutting foam materials. The focused laser beam can create intricate designs, sharp edges, and fine details with exceptional accuracy. CNC system guarantees processing reliability without manual error.
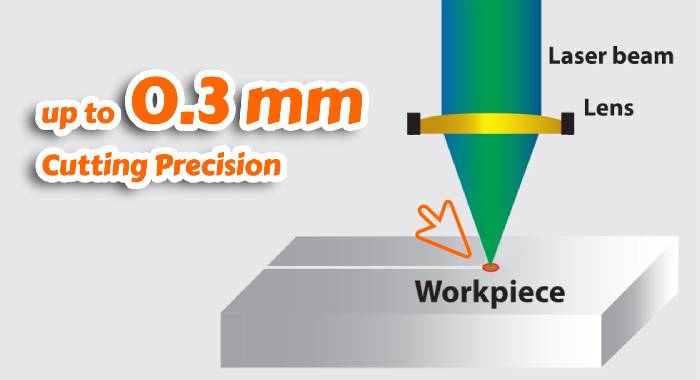
✦ Wide Materials Versatility
Foam laser cutters are versatile and can handle a wide range of foam types, densities, and thicknesses. They can cut through foam sheets, blocks, and 3D foam structures with ease. Besides foam materials, the laser cutter can handle other materials like felt, leather, and fabric. That will offer great convenience if you want to expand your industry.
Foam Types
You can laser cut
• Polyurethane Foam (PU): This is a common choice for laser cutting due to its versatility and use in applications like packaging, cushioning, and upholstery.
• Polystyrene Foam (PS): Expanded and extruded polystyrene foams are suitable for laser cutting. They are used in insulation, modeling, and crafting.
• Polyethylene Foam (PE): This foam is used for packaging, cushioning, and buoyancy aids.
• Polypropylene Foam (PP): It's often used in the automotive industry for noise and vibration control.
• Ethylene-Vinyl Acetate (EVA) Foam: EVA foam is widely used for crafting, padding, and footwear, and it's compatible with laser cutting and engraving.
• Polyvinyl Chloride (PVC) Foam: PVC foam is used for signage, displays, and model making and can be laser cut.
Foam Thickness
You can laser cut
* With the powerful and fine laser beam, the foam laser cutter can cut through thick foam up to 30mm.
✦ Clean and Sealed Edges
The clean and smooth cutting edge is the critical factor manufacturers always care about. Because of heat energy, the foam can be timely sealed on the edge, which guarantees the edge is intact while keeping scrip chipping from flying everywhere. Laser cutting foam produces clean and sealed edges without fraying or melting, resulting in professional-looking cuts. This eliminates the need for additional finishing processes and ensures a high-quality final product. This is significant for some applications having high standards in cutting precision, like medical instruments, industrial parts, gaskets, and protective devices.
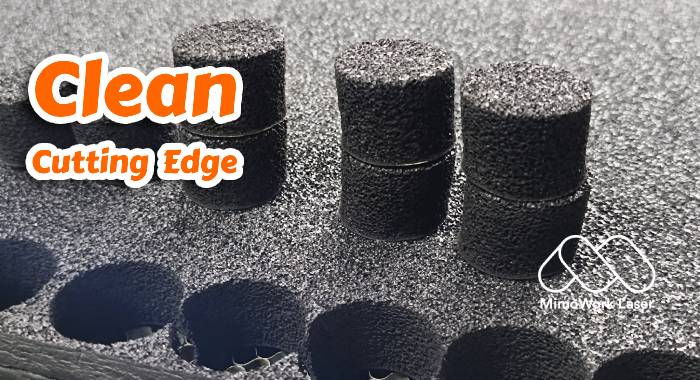
✦ High Efficiency
Laser cutting foam is a fast and efficient process. The laser beam cuts through the foam material quickly and precisely, allowing for rapid production and turnaround times. MimoWork designed various laser machine options and has different configurations you can upgrade, like dual laser heads, four laser heads, and servo motor. You can choose suitable laser configurations and options to further increase your production efficiency. Any questions you can consult our laser expert in your free time. Besides, the foam laser cutter is easy to operate, especially for a beginner, requires little learning cost. We will offer suitable laser machine solutions and corresponding installation and guide support. >> Talk with Us
✦ Minimal Material Waste
With the help of advanced laser cutting software(MIMOCut), the whole laser cutting foam process will get an optimal cutting arrangement. Foam laser cutters minimize material waste by optimizing the cutting path and reducing excess material removal. This efficiency helps save costs and resources, making laser cutting foam a sustainable option. If you have nesting requirement, there is auto-nesting software you can choose, helping simplifying the nesting process, enhancing your processing efficiency.
✦ Complex Shapes and Designs
Foam laser cutters can create complex shapes, intricate patterns, and detailed designs that would be difficult or impossible to achieve with traditional cutting methods. This capability opens up new possibilities for creative projects and applications.
✦ Non-Contact Cutting
Laser cutting foam is a non-contact process, meaning that the laser beam does not physically touch the foam surface. This reduces the risk of material deformation and ensures consistent cutting quality.
✦ Customization and Personalization
Foam laser cutters enable customization and personalization of foam products. They can cut custom shapes, logos, text, and graphics, making them ideal for branding, signage, packaging, and promotional items.
Popular Foam Laser Cutter
When you have decided to invest in a laser cutting machine for your foam production, you need to consider the foam material types, size, thickness and more to find a foam laser cutter with optimal configurations. The flatbed laser cutter for foam has a 1300mm * 900mm working area, is a entry-level foam laser cutter. For regular foam products like toolboxs, decorations, and crafts, the Flatbed Laser Cutter 130 is the most popular choice for foam cutting and engraving. The size and power satisfy most requirements, and the price is affordable. Pass through design, upgraded camera system, optional working table, and more machine configurations you can choose.
Machine Specification
Working Area (W *L) | 1300mm * 900mm (51.2” * 35.4 ”) |
Software | Offline Software |
Laser Power | 100W/150W/300W |
Laser Source | CO2 Glass Laser Tube or CO2 RF Metal Laser Tube |
Mechanical Control System | Step Motor Belt Control |
Working Table | Honey Comb Working Table or Knife Strip Working Table |
Max Speed | 1~400mm/s |
Acceleration Speed | 1000~4000mm/s2 |
Options: Upgrade Foam Production
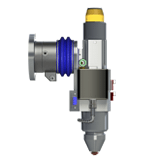
Auto Focus
You may need to set a certain focus distance in the software when the cutting material is not flat or with different thickness. Then the laser head will automatically go up and down, keeping the optimal focus distance to material surface.
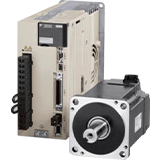
Servo Motor
A servomotor is a closed-loop servomechanism that uses position feedback to control its motion and final position.
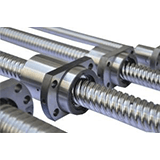
Ball Screw
In contrast to conventional lead screws, ball screws tend to be rather bulky, due to the need to have a mechanism to re-circulate the balls. The ball screw ensures high speed and high precision laser cutting.
Wide Applications

Learn More about the Foam Laser Cutter
If you have larger cutting patters or roll foam, the foam laser cutting machine 160 suits you. The Flatbed Laser Cutter 160 is a large-format machine. With the auto feeder and conveyor table, you can accomplish auto-processing roll materials. 1600mm *1000mm of working area is suitable for most yoga mat, marine mat, seat cushion, industrial gasket and more. Multiple laser heads are optional to enhance productivity. The enclosed design from fabric laser cutting machine ensures the safety of laser use. The emergency stop button, emergency signal light, and all electrical components are installed strictly according to CE standards.
Machine Specification
Working Area (W * L) | 1600mm * 1000mm (62.9” * 39.3 ”) |
Software | Offline Software |
Laser Power | 100W/150W/300W |
Laser Source | CO2 Glass Laser Tube or CO2 RF Metal Laser Tube |
Mechanical Control System | Belt Transmission & Step Motor Drive |
Working Table | Honey Comb Working Table / Knife Strip Working Table / Conveyor Working Table |
Max Speed | 1~400mm/s |
Acceleration Speed | 1000~4000mm/s2 |
Options: Upgrade Foam Production

Dual Laser Heads
In the simplest and most economic way to speed up your production efficiency is to mount multiple laser heads on the same gantry and cut the same pattern simultaneously. This doesn't take extra space or labor.
When you are trying to cut a whole lot of different designs and want to save material to the largest degree, the Nesting Software will be a good choice for you.
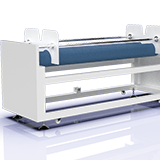
The Auto Feeder combined with the Conveyor Table is the ideal solution for series and mass production. It transports the flexible material (fabric most of the time) from the roll to the cutting process on the laser system.
Wide Applications

Start Your Foam Production with Flatbed Laser Cutter 160!
• Can you cut foam with a laser cutter?
Yes, foam can be cut with a laser cutter. Laser cutting foam is a common and effective process that offers several advantages, including precision, versatility, and efficiency. The focused laser beam vaporizes or melts the foam material along a predetermined path, resulting in clean and precise cuts with sealed edges.
• Can you laser cut eva foam?
Yes, EVA (ethylene-vinyl acetate) foam can be laser cut effectively. EVA foam is a versatile material commonly used in various industries such as footwear, packaging, crafts, and cosplay. Laser cutting EVA foam offers several advantages, including precise cuts, clean edges, and the ability to create intricate designs and shapes. The focused laser beam vaporizes the foam material along a predetermined path, resulting in accurate and detailed cuts without fraying or melting.
• How to laser cut foam?
1. Prepare the Laser Cutting Machine:
Ensure the laser cutting machine is properly set up and calibrated for cutting foam. Check the focus of the laser beam and adjust it if necessary for optimal cutting performance.
2. Choose the Right Settings:
Select the appropriate laser power, cutting speed, and frequency settings based on the type and thickness of the foam material you are cutting. Refer to the machine's manual or consult with the manufacturer for recommended settings.
3. Prepare the Foam Material:
Place the foam material on the laser cutting bed and secure it in place using clamps or a vacuum table to prevent movement during cutting.
4. Start the Laser Cutting Process:
Load the cutting file into the laser cutting machine's software and position the laser beam at the starting point of the cutting path.
Initiate the cutting process, and the laser beam will follow the predetermined path, cutting through the foam material along the way.
Get Benefits and Profits from Foam Laser Cutter, Talk with Us to learn more
Any Questions about Laser Cutting Foam?
Post time: May-09-2024