レーザーテクノロジーを初めて使用し、レーザー切断機の購入を検討する場合は、尋ねたい質問がたくさんある必要があります。
ミモウォークCO2レーザーマシンに関する詳細情報を共有できることを嬉しく思います。うまくいけば、米国からのレーザーサプライヤーからのものであろうと、本当に自分に合ったデバイスを見つけることができます。
この記事では、主流のマシン構成の簡単な概要を説明し、各セクターの比較分析を行います。一般に、この記事は以下のようにポイントをカバーします。
CO2レーザーマシンのメカニック
a。ブラシレスDCモーター、サーボモーター、ステップモーター

ブラシレスDC(直流)モーター
ブラシレスDCモーターは、高RPM(1分あたりの回転)で実行できます。 DCモーターの固定子は、回転する回転磁場を提供し、アーマチュアを回転させます。すべてのモーターの中で、ブラシレスDCモーターは最も強力な運動エネルギーを提供し、レーザーヘッドを途方もない速度で移動させることができます。Mimoworkの最高のCO2レーザー彫刻マシン ブラシレスモーターが装備されており、2000mm/sの最大彫刻速度に達することができます.ブラシレスDCモーターは、CO2レーザー切断機ではめったに見られません。これは、材料を切断する速度が材料の厚さによって制限されているためです。それどころか、あなたはあなたの素材にグラフィックを彫るために小さな力を必要とします、レーザー彫刻家を備えたブラシレスモーターは彫刻時間をより正確に短縮します。
サーボモーターとステップモーター
私たち全員が知っているように、サーボモーターは高速で高レベルのトルクを提供できるという事実を知っており、ステッパーモーターよりも高価です。サーボモーターには、位置制御のためにパルスを調整するためのエンコーダーが必要です。エンコーダーとギアボックスが必要になると、システムがより機械的に複雑になり、メンテナンスが頻繁になり、コストが高くなります。 CO2レーザーマシンと組み合わせて、サーボモーターは、ステッピングモーターよりもガントリーとレーザーヘッドの位置でより高い精度を実現できます。 率直に言って、ほとんどの場合、さまざまなモーターを使用する場合、特にあまり精度を必要としないシンプルなクラフトギフトを作る場合は、精度の違いを伝えるのは困難です。フィルタープレート用のフィルタークロス、車両の安全性インフレータブルカーテン、導体の絶縁カバーなどの複合材料と技術アプリケーションを処理している場合、サーボモーターの機能は完全に実証されます。
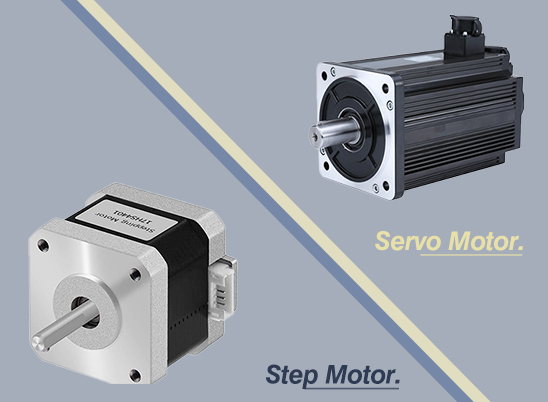
各モーターには長所と短所があります。あなたに合ったものはあなたにとって最高です。
確かに、ミモウォークはそれを提供できますCO2レーザー彫刻家とカッター 3種類のモーター付き要件と予算に基づいています。
b。ベルトドライブとギアドライブ
ベルトドライブはベルトでホイールを接続するシステムですが、ギアドライブは2つのギアが相互に接続されているため、2つのギアが互いに接続されています。レーザー機器の機械的構造では、両方のドライブが使用されますレーザーガントリーの動きを制御し、レーザーマシンの精度を定義しました。
2つを次の表と比較しましょう。
ベルトドライブ | ギアドライブ |
主な要素プーリーとベルト | メインの要素ギア |
より多くのスペースが必要です | 必要なスペースが少ないため、レーザーマシンは小さくなるように設計できます |
高い摩擦損失、したがって、伝播が低下し、効率が低下します | 摩擦損失が低いため、伝送が高く、効率が高くなります |
ギアドライブよりも平均寿命が少なく、通常3年ごとに変化します | ベルトドライブよりもはるかに大きな平均寿命、通常は10年ごとに変化します |
より多くのメンテナンスが必要ですが、メンテナンスコストは比較的安価で便利です | メンテナンスが少なくなりますが、メンテナンスコストは比較的大切で面倒です |
潤滑は必要ありません | 定期的な潤滑が必要です |
非常に静かな動作 | 騒々しい |
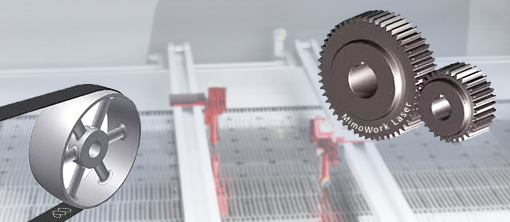
ギアドライブとベルトドライブシステムの両方は、長所と短所を備えたレーザー切断機で一般的に設計されています。単に要約して、ベルトドライブシステムは、小型の飛行光学的タイプのマシンでより有利です;伝送と耐久性が高いため、ギアドライブは、通常、ハイブリッド光学設計を備えた大型レーザーカッターにより適しています。
c。固定作業テーブルとコンベア作業テーブル
レーザー処理の最適化には、高品質のレーザー供給と、レーザーヘッドを移動するための優れた駆動システム以上のものが必要です。適切な材料サポートテーブルも必要です。素材またはアプリケーションに合わせて調整された作業テーブルは、レーザーマシンの可能性を最大化できることを意味します。
一般的に、作業プラットフォームには2つのカテゴリがあります。文房具とモバイルです。
charさまざまなアプリケーションでは、あらゆる種類の材料を使用することになります。シート材料またはコイル状の材料)
○固定作業テーブルアクリル、木材、紙(段ボール)などのシート材料を配置するのに最適です。
•ナイフストリップテーブル
•ハニーコームテーブル

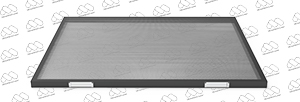
○コンベア作業テーブル生地、革、フォームなどのロールマテリアルを配置するのに最適です。
•シャトルテーブル
•コンベアテーブル
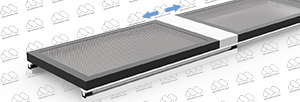
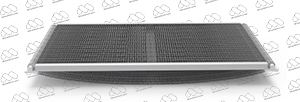
適切な作業テーブルデザインの利点
✔切断排出量の優れた抽出
✔材料を安定させ、切断するときに変位は発生しません
✔ワークピースをロードしてアンロードするのに便利です
✔フラットサーフェスのおかげで、最適なフォーカスガイダンス
✔シンプルなケアとクリーニング
d。自動リフティングと手動リフティングプラットフォーム
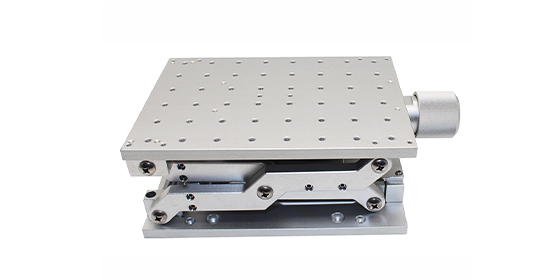
あなたがしっかりした材料を刻んでいるとき、アクリル(PMMA)そして木材(MDF), 材料の厚さは異なります。適切なフォーカスの高さは、彫刻効果を最適化できます。最小のフォーカスポイントを見つけるには、調整可能な作業プラットフォームが必要です。 CO2レーザー彫刻マシンの場合、自動リフティングと手動リフティングプラットフォームが一般的に比較されます。予算が適切な場合は、自動リフティングプラットフォームにアクセスしてください。切断と彫刻の精度を改善するだけでなく、大量の時間と労力を節約することもできます。
e。上、側面、下部の換気システム
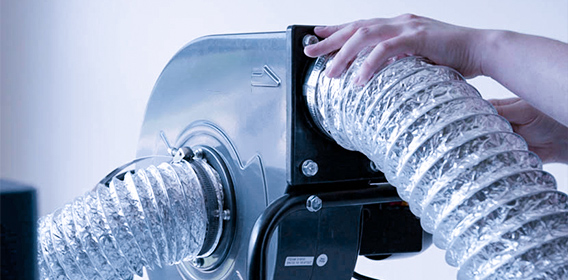
下部の換気システムは、CO2レーザーマシンの最も一般的な選択肢ですが、Mimoworkにはレーザー処理エクスペリエンス全体を進めるための他のタイプの設計もあります。 aの大規模なレーザー切断機、Mimoworkは組み合わせを使用します上部と下部の消耗システム高品質のレーザー切断結果を維持しながら抽出効果を高めるため。私たちの大部分のためにガルボマーキングマシン、インストールしますサイド換気システム煙を使い果たします。マシンのすべての詳細は、各業界の問題を解決するために、より適切に対象とする必要があります。
An 抽出システム機械加工された材料の下で生成されます。熱処理によって生成されたヒュームを抽出するだけでなく、材料、特に軽量生地も安定させます。処理される材料によって覆われている処理面の部分が大きいほど、吸引効果と結果として生じる吸引真空が高くなります。
CO2ガラスレーザーチューブ対CO2 RFレーザーチューブ
a。 CO2レーザーの励起原理
二酸化炭素レーザーは、開発される最も初期のガスレーザーの1つでした。数十年にわたる開発により、この技術は非常に成熟しており、多くのアプリケーションにとって十分です。 CO2レーザーチューブは、の原理を通してレーザーを興奮させます輝く放電そして電気エネルギーを濃縮光エネルギーに変換します。二酸化炭素(アクティブレーザー培地)およびレーザーチューブ内の他のガスに高電圧を塗布することにより、ガスは輝く放電を生成し、ミラーが位置する反射ミラーの間の容器で容器で継続的に励起されます。レーザーを生成する容器。
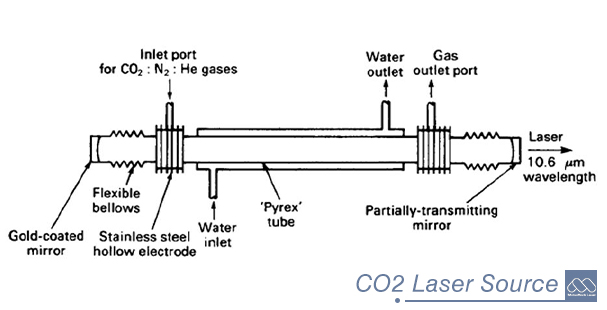
b。 CO2ガラスレーザーチューブとCO2 RFレーザーチューブの違い
CO2レーザーマシンをより包括的に理解したい場合は、詳細を掘り下げる必要があります。レーザーソース。非金属材料を処理するのに最も適したレーザータイプとして、CO2レーザー源は2つの主要なテクノロジーに分けることができます。ガラスレーザーチューブそしてRFメタルレーザーチューブ.
(ちなみに、高出力ファーストアキシャルフローCO2レーザーと遅いアキシアルフローCO2レーザーは、今日の議論の範囲内にありません)
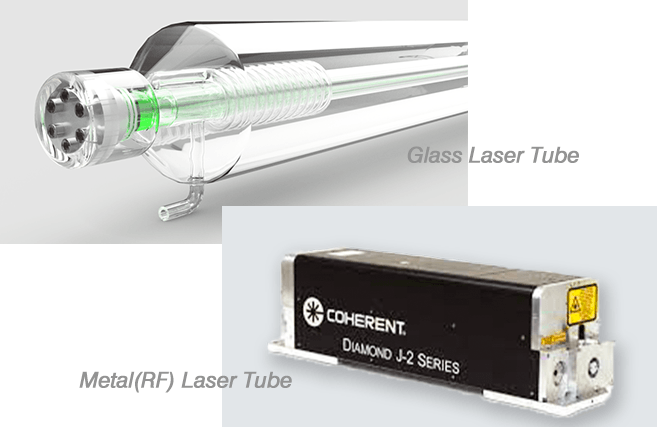
ガラス(DC)レーザーチューブ | 金属(RF)レーザーチューブ | |
寿命 | 2500-3500時間 | 20,000時間 |
ブランド | 中国語 | 筋の通った |
冷却方法 | 寒さ | 寒さ |
充電式 | いいえ、一度に使用するだけです | はい |
保証 | 6ヶ月 | 12か月 |
制御システムとソフトウェア
制御システムは機械機械の脳であり、CNC(コンピューター数値制御)プログラミング言語を使用してレーザーに移動する場所をレーザーに指示します。また、制御システムは、レーザーソースの出力を制御および調整して、レーザーカットテクノロジーを記述するために一般的に使用される柔軟な生産を実現します。レーザーマシンは、あるデザインの製造から別の設計に迅速に切り替えることができるだけでなく、また、ツールを変更せずにレーザーパワーと切削速度の設定を変更するだけで、さまざまな材料を処理できます。
市場の多くは、中国のソフトウェア技術とヨーロッパおよびアメリカのレーザー企業のソフトウェア技術を比較します。単にカットしてパターンを刻むために、市場に出回っているほとんどのソフトウェアのアルゴリズムはそれほど違いはありません。多数のメーカーからの長年のデータフィードバックがあるため、当社のソフトウェアには以下の機能があります。
1。使いやすい
2。長期的に安定した安全な動作
3.生産時間を効率的に評価します
4。DXF、AI、PLTおよびその他の多くのファイルをサポートします
5。変更の可能性を備えた複数の切断ファイルを一度にインポートする
6.列の配列と行のある列と行のある切断パターンを自動アレンジしますミモネスト
通常の切断ソフトウェアの基礎に加えて、ビジョン認識システム生産の自動化の程度を改善し、労働を減らし、切断精度を改善できます。簡単に言えば、CO2レーザーマシンに設置されたCCDカメラまたはHDカメラは、人間の目のように機能し、レーザーマシンにどこで切断するかを指示します。このテクノロジーは、染色出版スポーツウェア、屋外旗、刺繍パッチなどのデジタル印刷アプリケーションや刺繍分野で一般的に使用されています。 Mimoworkが提供できる視覚認識方法には3種類あります。
contour等高線認識
デジタル印刷と昇華印刷製品が人気を博しています。いくつかの昇華スポーツウェア、印刷されたバナー、ティアドロップのように、これらの生地のパターンは、伝統的なナイフカッターや手動のはさみによってカットされていません。パターンの輪郭切断の高い要件は、視力レーザーシステムの強度にすぎません。輪郭認識システムを使用すると、レーザーカッターは、HDカメラで写真を撮った後、輪郭に沿って正確に切断できます。ファイルを切断し、トリミング後の輪郭レーザー切断は、切断品質と生産効率を大幅に向上させる必要はありません。
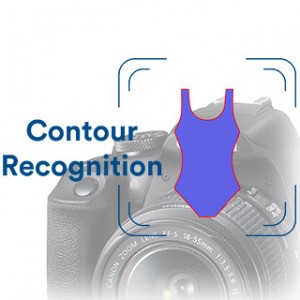
オペレーションガイド:
1. パターン化された製品を供給します>
2. パターンの写真を撮ります>
3. 輪郭レーザー切断を開始>
4. 完成した>を収集します
▮登録マークポイント
CCDカメラ正確な切断でレーザーを支援するために、木材のボードに印刷されたパターンを認識して見つけることができます。木材の看板、プラーク、アートワーク、印刷された木材で作られた木材の写真は、簡単に処理できます。
ステップ1。
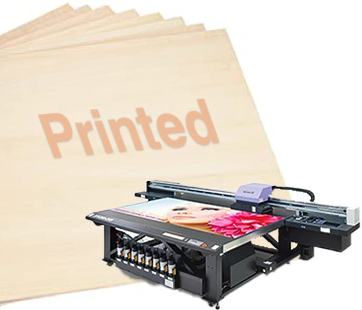
>>木製のボードにパターンを直接印刷します
ステップ2。
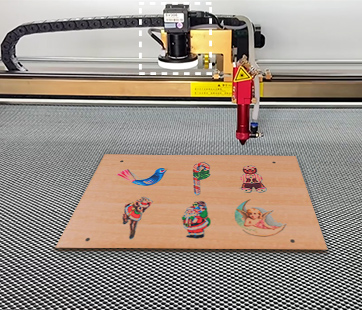
>> CCDカメラはレーザーがデザインをカットするのを支援します
ステップ3。
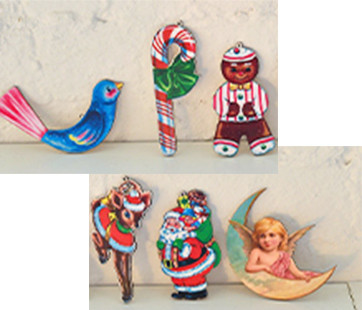
>>完成した作品を集めます
▮テンプレートマッチング
いくつかのパッチ、ラベル、同じサイズとパターンの印刷されたフォイルの場合、Mimoworkのテンプレートマッチングビジョンシステムは非常に役立ちます。レーザーシステムは、さまざまなパッチの特徴部分に一致する設計切断ファイルであるセットテンプレートを認識して配置することにより、小さなパターンを正確にカットできます。パターン、ロゴ、テキスト、またはその他の視覚的認識可能な部分が機能部分になります。
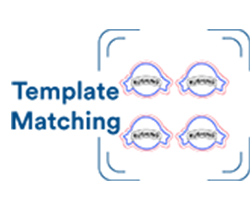
レーザーオプション
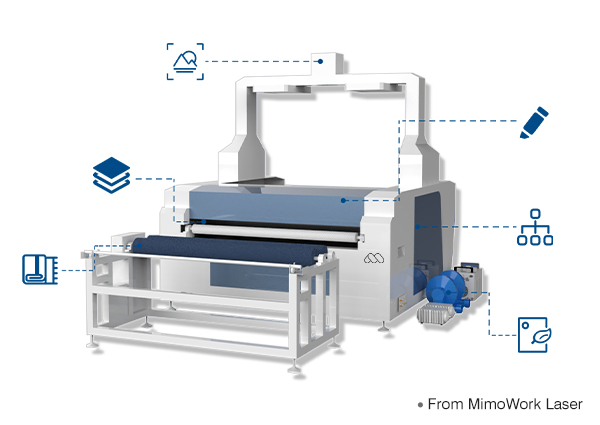
Mimoworkは、各アプリケーションに従って厳密に基本的なレーザーカッターに多数の追加オプションを提供しています。毎日の生産プロセスでは、レーザーマシンのこれらのカスタマイズされた設計は、市場の要件に応じて製品の品質と柔軟性を向上させることを目指しています。私たちとの早期コミュニケーションにおける最も重要なリンクは、あなたの生産状況、現在生産で使用されているツール、および生産でどのような問題が発生するかを知ることです。それでは、好まれるいくつかの一般的なオプションコンポーネントを紹介しましょう。
a。複数のレーザーヘッドを選択できます
1つのマシンに複数のレーザーヘッドとチューブを追加することは、生産効率を高めるための最も簡単でコスト削減方法です。複数のレーザーカッターを一度に購入することと比較すると、複数のレーザーヘッドを設置すると、投資コストと作業スペースが節約されます。ただし、あらゆる状況で複数レーザーヘッドは適切ではありません。また、作業テーブルのサイズとパターンのサイズを切断することも考慮する必要があります。したがって、購入する前に、顧客がいくつかのデザインの例を送信することがよくあります。
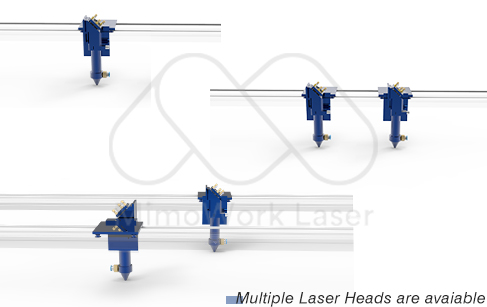
レーザーマシンまたはレーザーメンテナンスに関するその他の質問
投稿時間:10月12〜2021年