Laser Cut Glass: All you Need to Know About [2024]
When most people think of glass, they imagine it as a delicate material - something that can easily break if subjected to too much force or heat.
For this reason, it may come as a surprise to learn that glass can in fact be cut using a laser.
Through a process known as laser ablation, high-powered lasers can precisely remove or "cut" shapes from glass without causing cracks or fractures.
Table of Content:
1. Can you Laser Cut Glass?
Laser ablation works by directing an extremely focused laser beam onto the surface of the glass.
The intense heat from the laser vaporizes a tiny amount of the glass material.
By moving the laser beam according to a programmed pattern, intricate shapes, and designs can be cut with amazing accuracy, sometimes down to a resolution of just a few thousandths of an inch.
Unlike mechanical cutting methods which rely on physical contact, lasers allow for non-contact cutting that produces very clean edges without chipping or stress on the material.
While the idea of "cutting" glass with a laser may seem counterintuitive, it is possible because lasers allow for an extremely precise and controlled heating and removal of material.
As long as the cutting is done gradually in small increments, the glass is able to dissipate heat quickly enough that it does not crack or explode from thermal shock.
This makes laser cutting an ideal process for glass, allowing intricate patterns to be produced that would be difficult or impossible with traditional cutting methods.
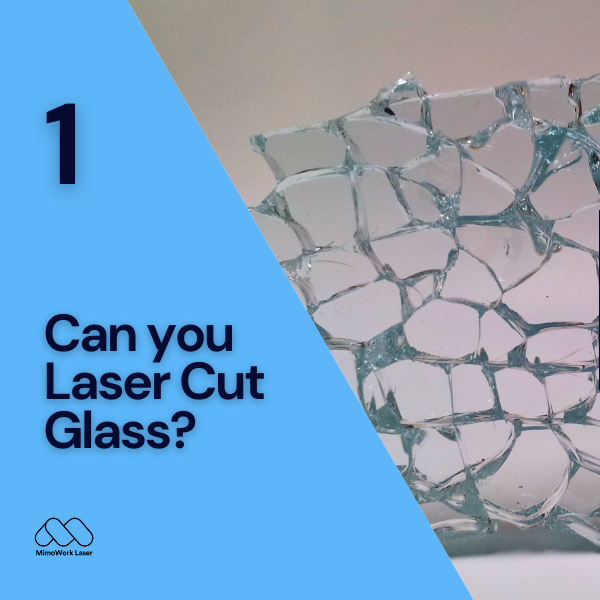
2. What Glass can be Laser Cut?
Not all types of glass can be laser cut equally well. The optimal glass for laser cutting needs to have certain thermal and optical properties.
Some of the most common and suitable types of glass for laser cutting include:
1. Annealed Glass: Plain float or plate glass that has not undergone any additional heat treatment. It cuts and engraves well but is more prone to cracking from thermal stress.
2. Tempered Glass: Glass that has been heat-treated for increased strength and shatter resistance. It has a higher thermal tolerance but increased cost.
3. Low-iron Glass: Glass with reduced iron content which transmits laser light more efficiently and cuts with less residual heat effects.
4. Optical Glass: Specialty glass formulated for high light transmission with low attenuation, used for precision optics applications.
5. Fused Silica Glass: An extremely high-purity form of quartz glass that can withstand high laser power and cuts/etches with unsurpassed precision and detail.
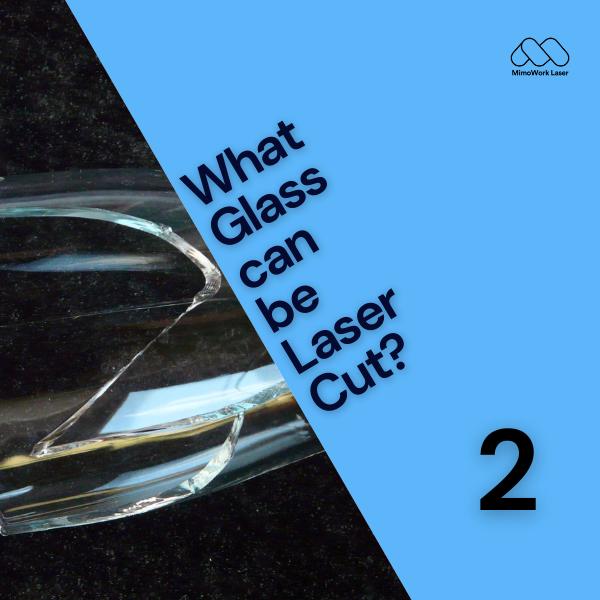
In general, glasses with lower iron content are cut with higher quality and efficiency as they absorb less laser energy.
Thicker glasses above 3mm also require more powerful lasers. The composition and processing of the glass determine its suitability for laser cutting.
3. What Laser can Cut Glass?
There are several types of industrial lasers suitable for cutting glass, with the optimal choice depending on factors like material thickness, cutting speed, and precision requirements:
1. CO2 Lasers: The workhorse laser for cutting various materials including glass. Produces an infrared beam well-absorbed by most materials. It can cut up to 30mm of glass but at slower speeds.
2. Fiber Lasers: Newer solid-state lasers offering faster cutting speeds than CO2. Produce near-infrared beams efficiently absorbed by glass. Commonly used for cutting up to 15mm glass.
3. Green Lasers: Solid-state lasers emitting visible green light well-absorbed by glass without heating the surrounding areas. Used for high-precision engraving of thin glass.
4. UV Lasers: Excimer lasers emitting ultraviolet light can achieve the highest cutting precision on thin glasses due to minimal heat-affected zones. However, requires more complex optics.
5. Picosecond Lasers: Ultrafast pulsed lasers that cut via ablation with individual pulses only a trillionth of a second long. It can cut extremely intricate patterns in glass with almost no heat or cracking risks.
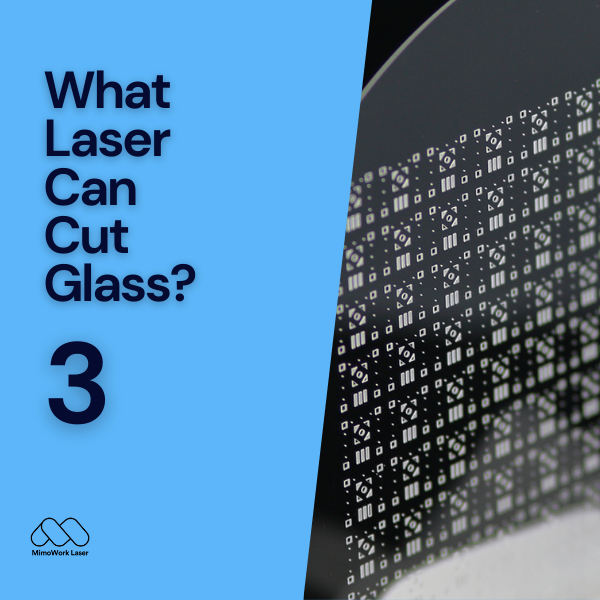
The right laser depends on factors like the glass thickness and thermal/optical properties, as well as the required cutting speed, precision, and edge quality.
With the appropriate laser setup, however, almost any type of glass material can be cut into beautiful, intricate patterns.
4. Advantages of Laser Cutting Glass
There are several key advantages that come with using laser cutting technology for glass:
1. Precision & Detail: Lasers allow for micron-level precision cutting of intricate patterns and complex shapes that would be difficult or impossible with other methods. This makes laser cutting ideal for logos, delicate artwork, and precision optics applications.
2. No Physical Contact: Since lasers cut through ablation rather than mechanical forces, there is no contact or stress placed on the glass during cutting. This reduces the chances of cracking or chipping even with fragile or delicate glass materials.
3. Clean Edges: The laser cutting process vaporizes the glass very cleanly, producing edges that are often glass-like or mirror-finished without any mechanical damage or debris.
4. Flexibility: Laser systems can be easily programmed to cut a wide variety of shapes and patterns through digital design files. Changes can also be made quickly and efficiently through software without switching physical tooling.
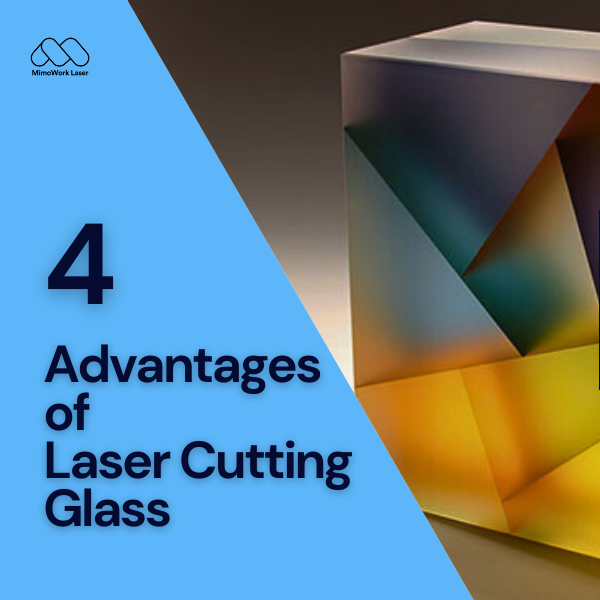
5. Speed: While not as fast as mechanical cutting for bulk applications, laser cutting speeds continue to increase with newer laser technologies. Intricate patterns that once took hours can now be cut in minutes.
6. No Tool Wear: Since lasers function through optical focusing rather than mechanical contact, there is no tool wear, breakage, or need for frequent replacement of cutting edges like with mechanical processes.
7. Material Compatibility: Properly configured laser systems are compatible with cutting almost any type of glass, from common soda lime glass to specialty fused silica, with results only limited by the material's optical and thermal properties.
5. Disadvantages of Glass Laser Cutting
Of course, laser cutting technology for glass is not without some drawbacks:
1. High Capital Costs: While laser operation costs can be modest, the initial investment for a full industrial laser cutting system suitable for glass can be substantial, limiting accessibility for small shops or prototype work.
2. Throughput Limitations: Laser cutting is generally slower than mechanical cutting for bulk, commodity cutting of thicker glass sheets. Production rates may not be suitable for high-volume manufacturing applications.
3. Consumables: Lasers require periodic replacement of optical components that can degrade over time from exposure. Gas costs are also involved in assisted laser-cutting processes.
4. Material Compatibility: While lasers can cut many glass compositions, those with higher absorption may scorch or discolor rather than cut cleanly due to residual heat effects in the heat-affected zone.
5. Safety Precautions: Strict safety protocols and enclosed laser cutting cells are required to prevent eye and skin damage from high-power laser light and glass debris. Proper ventilation is also needed to remove noxious vapors.
6. Skill Requirements: Qualified technicians with laser safety training are required to operate laser systems. Proper optical alignment and process parameter optimization must also be performed regularly.
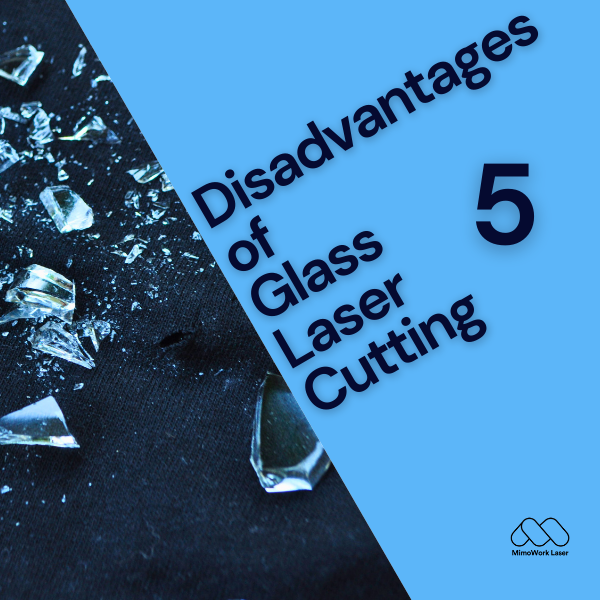
So in summary, while laser cutting enables new possibilities for glass, its advantages come at the cost of higher equipment investment and operating complexity compared to traditional cutting methods.
Careful consideration of an application's needs is important.
6. FAQs of Laser Glass Cutting
1. What Type of Glass Produces the Best Results for Laser Cutting?
Low-iron glass compositions tend to produce the cleanest cuts and edges when laser cut. Fused silica glass also performs very well due to its high purity and optical transmission properties.
In general, glass with lower iron content cuts more efficiently since it absorbs less laser energy.
2. Can Tempered Glass be Laser Cut?
Yes, tempered glass can be laser cut but requires more advanced laser systems and process optimization. The tempering process increases the thermal shock resistance of the glass, making it more tolerant of the localized heating from laser cutting.
Higher power lasers and slower cutting speeds are usually needed.
3. What is the Minimum Thickness I can Laser Cut?
Most industrial laser systems used for glass can reliably cut substrate thicknesses down to 1-2mm depending on the material composition and laser type/power. With specialized short-pulse lasers, cutting glass as thin as 0.1mm is possible.
The minimum cuttable thickness ultimately depends on the application needs and laser capabilities.
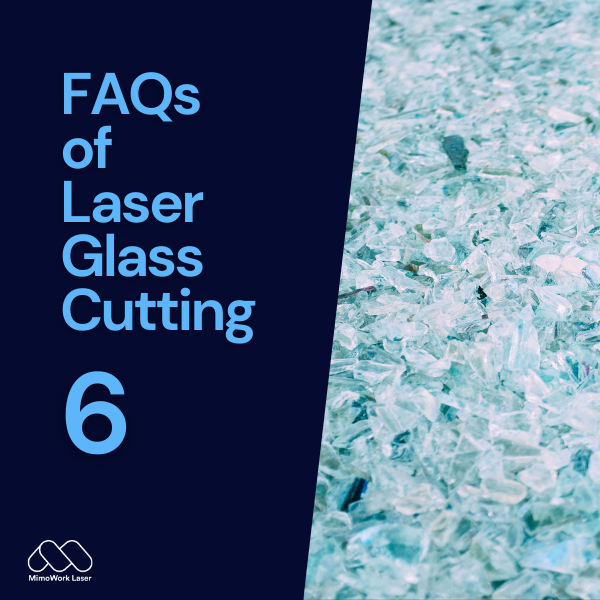
4. How Precise can Laser Cutting be for Glass?
With the proper laser and optics setup, resolutions of 2-5 thousandths of an inch can routinely be achieved when laser cutting/engraving on glass.
Even higher precision down to 1 thousandth of an inch or better is possible using ultrafast pulsed laser systems. The precision depends largely on factors like laser wavelength and beam quality.
5. Is the Cut Edge of Laser Cut Glass Safe?
Yes, the cut edge of the laser-ablated glass is generally safe since it is a vaporized edge rather than a chipped or stressed edge.
However, as with any glass-cutting process, proper handling precautions should still be observed, especially around tempered or toughened glass which can still pose risks if damaged post-cutting.
6. Is it Difficult to Design Patterns for Laser Cutting Glass?
No, pattern design for laser cutting is quite straightforward. Most laser cutting software uses standard image or vector file formats that can be created using common design tools.
The software then processes these files to generate cut paths while performing any needed nesting/arranging of parts on the sheet material.
We Don't Settle for Mediocre Results, Neither Should You
▶ About Us - MimoWork Laser
Elevate your Production with Our Highlights
Mimowork is a results-oriented laser manufacturer, based in Shanghai and Dongguan China, bringing 20-year deep operational expertise to produce laser systems and offer comprehensive processing and production solutions to SMEs (small and medium-sized enterprises) in a wide array of industries.
Our rich experience of laser solutions for metal and non-metal material processing is deeply rooted in worldwide advertisement, automotive & aviation, metalware, dye sublimation applications, fabric and textiles industry.
Rather than offering an uncertain solution that requires purchase from unqualified manufacturers, MimoWork controls every single part of the production chain to make sure our products have constant excellent performance.

MimoWork has been committed to the creation and upgrade of laser production and developed dozens of advanced laser technology to further improve clients' production capacity as well as great efficiency. Gaining many laser technology patents, we are always concentrating on the quality and safety of laser machine systems to ensure consistent and reliable processing production. The laser machine quality is certificated by CE and FDA.
Get More Ideas from Our YouTube Channel
You Might be Interested in:
We Accelerate in the Fast Lane of Innovation
Post time: Feb-14-2024