The basic laser welding process involves focusing a laser beam onto the joint area between two materials using an optical delivery system. When the beam contacts the materials, it transfers its energy, rapidly heating and melting a small area.
Table of Content
1. What is a Laser Welding Machine?
A laser welding machine is an industrial tool that utilizes a laser beam as a concentrated heat source to join multiple materials together.
Some key characteristics of laser welding machines include:
1. Laser Source: Most modern laser welders use solid-state laser diodes that produce a high-power laser beam in the infrared spectrum. Common laser sources include CO2, fiber, and diode lasers.
2. Optics: The laser beam travels through a series of optical components like mirrors, lenses, and nozzles that focus and direct the beam to the weld area with precision. Telescoping arms or gantries position the beam.
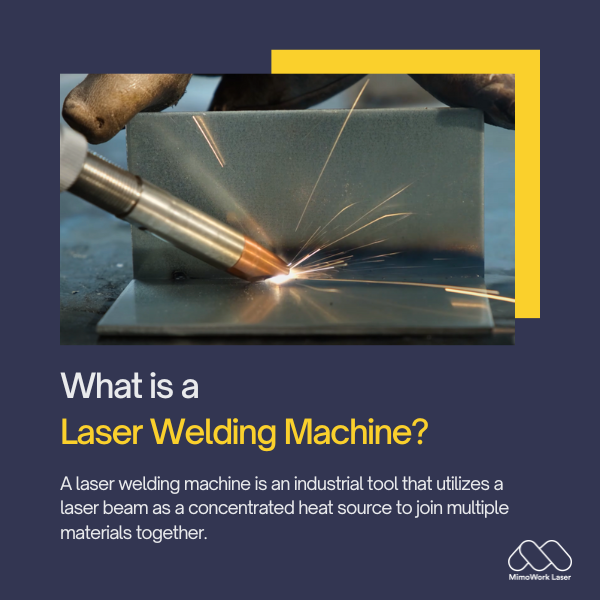
3. Automation: Many laser welders feature computer numerical control (CNC) integration and robotics to automate complex welding patterns and processes. Programmable paths and feedback sensors ensure accuracy.
4. Process Monitoring: Integrated cameras, spectrometers, and other sensors monitor the welding process in real-time. Any issues with beam alignment, penetration, or quality can be quickly detected and addressed.
5. Safety Interlocks: Protective housings, doors, and e-stop buttons safeguard operators from the high-powered laser beam. Interlocks shut down the laser if safety protocols are breached.
So in summary, a laser welding machine is a computer-controlled, industrial precision tool that utilizes a focused laser beam for automated, repeatable welding applications.
2. How Does Laser Welding Work?
Some key stages in the laser welding process include:
1. Laser Beam Generation: A solid-state laser diode or other source produces an infrared beam.
2. Beam Delivery: Mirrors, lenses, and a nozzle precisely focus the beam to a tight spot on the workpiece.
3. Material Heating: The beam rapidly heats the material, with a density approaching 106 W/cm2.
4. Melting and Joining: A small melt pool forms where the materials fuse. As the pool solidifies, a weld joint is created.
5. Cooling and Re-solidification: The weld area cools at high rates above 104°C/second, creating a fine-grained, hardened microstructure.
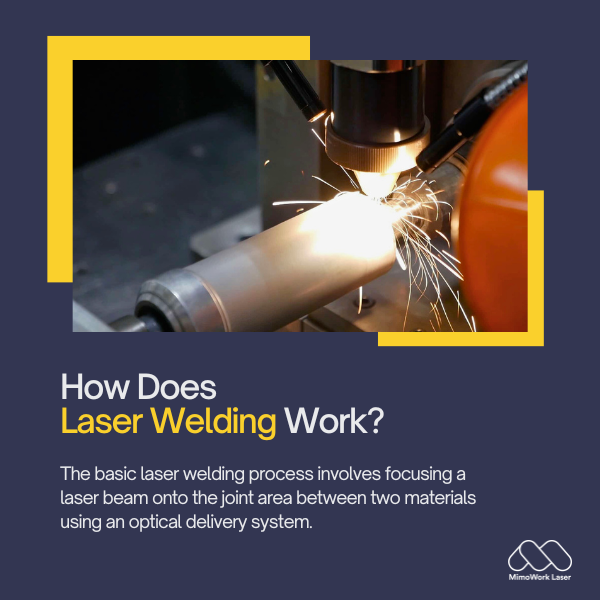
6. Progression: The beam moves or the parts are repositioned and the process repeats to complete the weld seam. Inert shielding gas may also be used.
So in summary, laser welding uses an intensely focused laser beam and controlled thermal cycling to produce high-quality, low heat-affected zone welds.
We Provided Helpful Information on Laser Welding Machines
As Well as Customized Solutions For your Business
3. Is Laser Welding better than MIG?
When compared to traditional metal inert gas (MIG) welding processes...
Laser welding offers several advantages:
1. Precision: Laser beams can be focused to a tiny 0.1-1mm spot, enabling very precise, repeatable welds. This is ideal for small, high-tolerance parts.
2. Speed: Welding rates for the laser are much faster than MIG, especially on thinner gauges. This improves productivity and reduces cycle times.
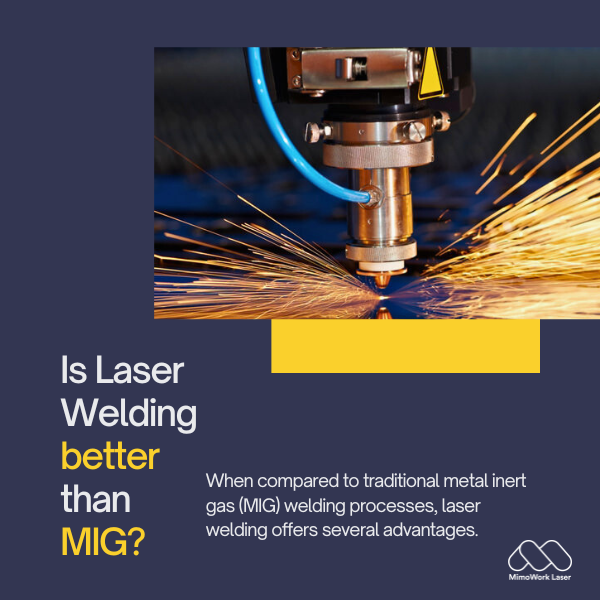
3. Quality: The concentrated heat source produces minimal distortion and narrow heat-affected zones. This results in strong, high-quality welds.
4. Automation: Laser welding is readily automated using robotics and CNC. This enables complex patterns and improved consistency vs manual MIG welding.
5. Materials: Lasers can join many material combinations, including multi-material and dissimilar metal welds.
However, MIG welding does have some advantages over laser in other applications:
1. Cost: MIG equipment has a lower initial investment cost than laser systems.
2. Thicker materials: MIG is better suited for welding thicker steel sections above 3mm, where laser absorption can be problematic.
3. Shielding gas: MIG uses an inert gas shield to protect the weld area, while laser often uses a sealed beam path.
So in summary, laser welding is generally preferred for precision, automation, and welding quality.
But MIG remains competitive for the production of thicker gauges on a budget.
The right process depends on the specific welding application and part requirements.
4. Is Laser Welding Better than TIG Welding?
Tungsten inert gas (TIG) welding is a manual, artistically skilled process that can produce excellent results on thin materials.
However, laser welding has some advantages over TIG:
1. Speed: Laser welding is significantly faster than TIG for production applications due to its automated precision. This improves throughput.
2. Precision: The focused laser beam allows positioning accuracy to within hundredths of a millimeter. This can't be matched by a human hand with TIG.
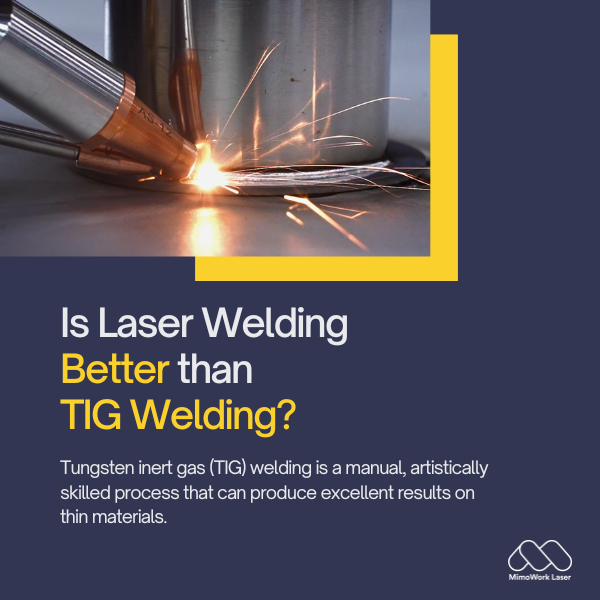
3. Control: Process variables like heat input and weld geometry are tightly controlled with a laser, ensuring consistent results batch over batch.
4. Materials: TIG is best for thinner conductive materials, while laser welding opens up a wider variety of multi-material combinations.
5. Automation: Robotic laser systems enable completely automated welding without fatigue, whereas TIG generally requires an operator's full attention and expertise.
However, TIG welding maintains an advantage for thin-gauge precision work or alloy welding where heat input must be carefully modulated. For these applications a skilled technician's touch is valuable.
5. What is the Disadvantage of Laser Welding?
As with any industrial process, laser welding does have some potential downsides to consider:
1. Cost: While becoming more affordable, high-power laser systems require a significant capital investment compared to other welding methods.
2. Consumables: Gas nozzles and optics degrade over time and must be replaced, adding to the cost of ownership.
3. Safety: Strict protocols and enclosed safety housings are required to prevent exposure to the high-intensity laser beam.
4. Training: Operators need training to work safely and properly maintain laser welding equipment.
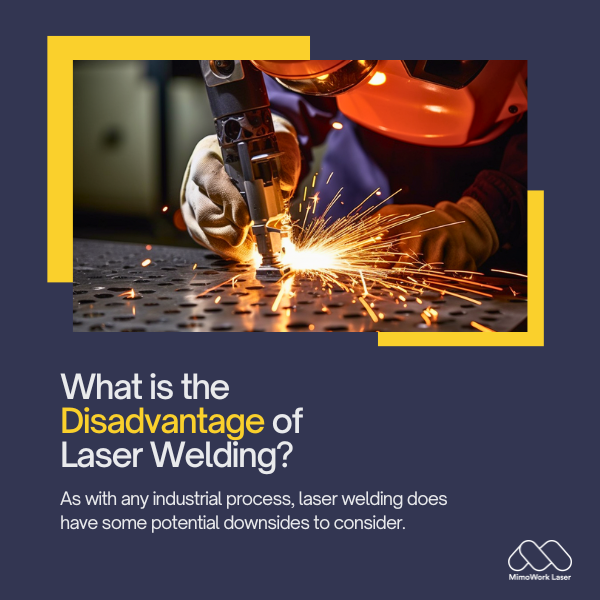
5. Line of sight: The laser beam travels in straight lines, so complex geometries may require multiple beams or workpiece repositioning.
6. Absorptivity: Certain materials like thick steel or aluminum can be difficult to weld if they don't absorb the laser's specific wavelength efficiently.
With proper precautions, training, and process optimization, however, laser welding delivers productivity, precision, and quality advantages for many industrial applications.
6. Does Laser Welding Need Gas?
Unlike gas-shielded welding processes, laser welding does not require the use of an inert shielding gas flowing over the weld area. This is because:
1. The focused laser beam travels through the air to create a small, high-energy weld pool that melts and joins the materials.
2. Surrounding air is not ionized like a gas plasma arc and does not interfere with the beam or weld formation.
3. The weld solidifies so rapidly from the concentrated heat that it forms before oxides can form on the surface.
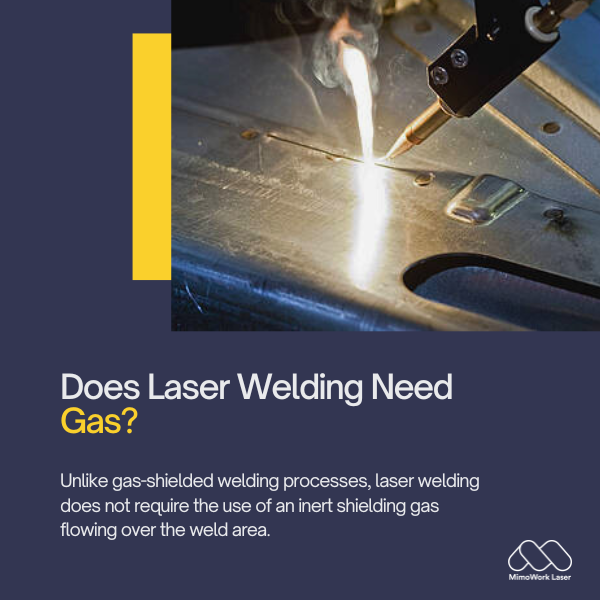
However, certain specialized laser welding applications may still benefit from using an assist gas:
1. For reactive metals like aluminum, gas shields the hot weld pool from oxygen in the air.
2. On high-powered laser jobs, gas stabilizes the plasma plume that forms during deep penetration welds.
3. Gas jets clear away fumes and debris for better beam transmission on dirty or painted surfaces.
So in summary, while not strictly necessary, inert gas may provide advantages for specific challenging laser welding applications or materials. But the process can often perform well without it.
▶ What Materials can be Laser Welded?
Nearly all metals can be laser welded including steel, aluminum, titanium, nickel alloys, and more.
Even dissimilar metal combinations are possible. The key is they must absorb the laser wavelength efficiently.
▶ How Thick of Materials can be Welded?
Sheets as thin as 0.1mm and as thick as 25mm can typically be laser welded, depending on the specific application and laser power.
Thicker sections may require multi-pass welding or special optics.
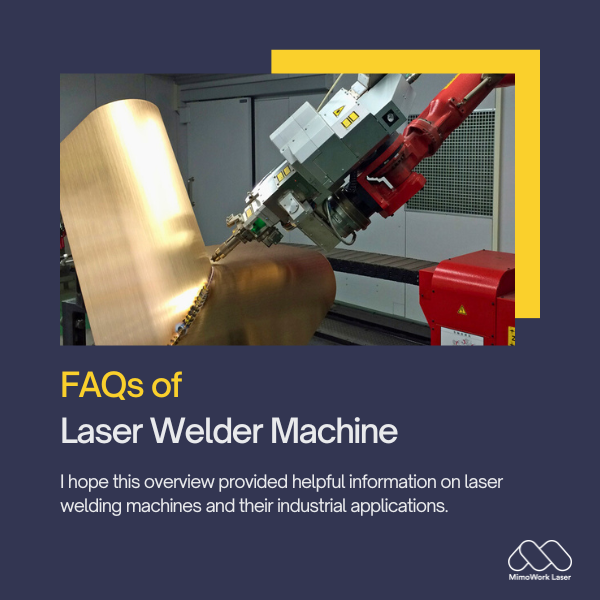
▶ Is Laser Welding Suitable for High Volume Production?
Absolutely. Robotic laser welding cells are commonly used in high-speed, automated production environments for applications like automotive manufacturing.
Throughput rates of several meters per minute are achievable.
▶ What Industries use Laser Welding?
Common laser welding applications can be found in automotive, electronics, medical devices, aerospace, tool/die, and small precision part manufacturing.
The technology is continuously expanding into new sectors.
▶ How do I choose a laser welding system?
Factors to consider include workpiece materials, size/thickness, throughput needs, budget, and required weld quality.
Reputable suppliers can help specify the right laser type, power, optics, and automation for your specific application.
▶ What Types of Welds can be Made?
Typical laser welding techniques include butt, lap, fillet, piercing, and cladding welds.
Some innovative methods like laser additive manufacturing are also emerging for repair and prototyping applications.
▶ Is Laser Welding Suitable for Repair Work?
Yes, laser welding is well-suited for precision repair of high-value components.
The concentrated heat input minimizes additional damage to the base materials during repair.
Want to Get Started with a Laser Welder Machine?
Why not Consider Us?
Post time: Feb-12-2024