1. Cutting Speed
Many customers in the consultation of laser cutting machine will ask how fast the laser machine can cut. Indeed, a laser cutting machine is highly efficient equipment, and cutting speed is naturally the focus of customer concern. But the fastest cutting speed doesn’t define the quality of laser cutting.
Too fast the cutting speed
a. Can’t cut through the material
b. The cutting surface presents oblique grain, and the lower half of the workpiece produces melting stains
c. Rough cutting edge
Too slow the cutting speed
a. Over melting condition with the rough cutting surface
b. Wider cutting gap and the sharp corner are melted into rounded corners
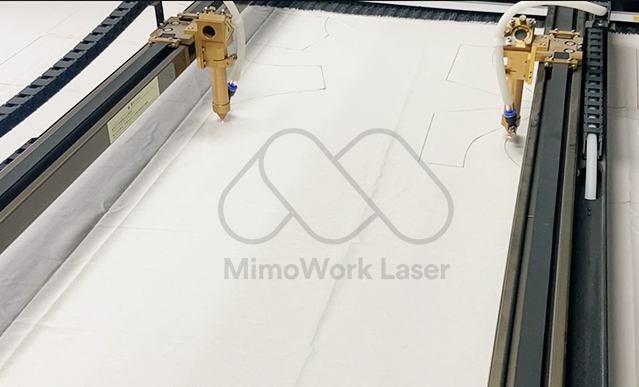
To make the laser cutting machine equipment better play its cutting function, do not simply ask how fast the laser machine can cut, the answer is often inaccurate. On the contrary, provide MimoWork with the specification of your material, and we will give you a more responsible answer.
2. Focus Point
Because the laser power density has a great influence on the cutting speed, the choice of lens focal length is an important point. The laser spot size after laser beam focusing is proportional to the focal length of the lens. After the laser beam is focused by the lens with a short focal length, the size of the laser spot is very small and the power density at the focal point is very high, which is beneficial to material cutting. But its disadvantage is that with short focus depth, only a small adjustment allowance for the thickness of the material. In general, a focus lens with a short focal length is more suitable for high-speed cutting thin material. And the focus lens with a long focal length has a wide focal depth, as long as it has enough power density, it is more suitable for cutting thick workpieces like foam, acrylic, and wood.
After determining which focal length lens to use, the relative position of the focal point to the workpiece surface is very important to ensure the cutting quality. Because of the highest power density at the focal point, in most cases, the focal point is just at or slightly below the surface of the workpiece when cutting. In the whole cutting process, it is an important condition to ensure that the relative position of focus and workpiece is constant to obtain stable cutting quality.
3. Air Blowing System & Auxiliary Gas
In general, material laser cutting requires the use of auxiliary gas, mainly related to the type and pressure of auxiliary gas. Usually, the auxiliary gas is ejected coaxially with the laser beam to protect the lens from contamination and blow away the slag at the bottom of the cutting area. For non-metallic materials and some metallic materials, compressed air or inert gas is used to remove melted and evaporated materials, while inhibiting excessive combustion in the cutting area.
Under the premise of ensuring auxiliary gas, gas pressure is an extremely important factor. When cutting thin material at high speed, high gas pressure is required to prevent slag from sticking to the back of the cut (hot slag will damage the cut edge when it hits the workpiece). When the material thickness increases or the cutting speed is slow, the gas pressure should be appropriately reduced.
4. Reflection Rate
The wavelength of the CO2 laser is 10.6 μm which is great for non-metallic materials to absorb. But the CO2 laser is not suitable for metal cutting, especially the metal material with high reflectivities like gold, silver, copper and aluminum metal, etc.
The absorption rate of the material to the beam plays an important role in the initial stage of heating, but once the cutting hole is formed inside the workpiece, the black-body effect of the hole makes the absorption rate of the material to the beam close to 100%.
The surface state of the material directly affects the absorption of the beam, especially the surface roughness, and the surface oxide layer will cause obvious changes in the absorption rate of the surface. In the practice of laser cutting, sometimes the cutting performance of the material can be improved by the influence of the material surface state on the beam absorption rate.
5. Laser Head Nozzle
If the nozzle is improperly selected or poorly maintained, it is easy to cause pollution or damage, or due to the bad roundness of the nozzle mouth or local blockage caused by hot metal splashing, eddy currents will be formed in the nozzle, resulting in significantly worse cutting performance. Sometimes, the nozzle mouth is not in line with the focused beam, forming the beam to shear the nozzle edge, which will also affect the edge cutting quality, increase the slit width and make the cutting size dislocation.
For nozzles, two issues should be paid special attention to
a. Influence of nozzle diameter.
b. Influence of the distance between the nozzle and the workpiece surface.
6. Optical Path
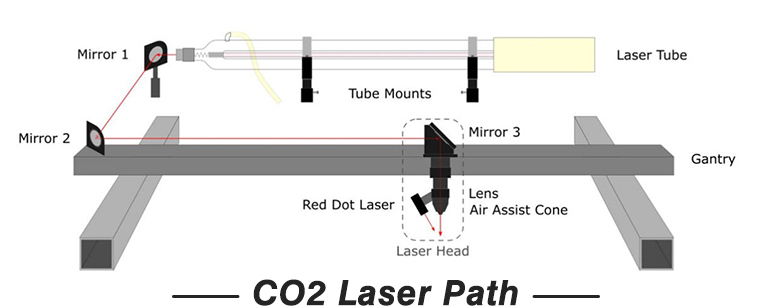
The original beam emitted by the laser is transmitted (including reflection and transmission) through the external optical path system, and accurately illuminates the surface of the workpiece with extremely high-power density.
The optical elements of the external optical path system should be regularly checked and adjusted in time to ensure that when the cutting torch is running above the workpiece, the light beam is correctly transmitted to the center of the lens and focused into a small spot to cut the workpiece with high quality. Once the position of any optical element changes or is contaminated, the cutting quality will be affected, and even the cutting can not be carried out.
The external optical path lens is polluted by impurities in the airflow and bonded by splashing particles in the cutting area, or the lens is not cooled enough, which will cause the lens to overheat and affect the beam energy transmission. It causes the collimation of the optical path to drift and leads to serious consequences. The lens overheating will also produce focal distortion and even endanger the lens itself.
Learn more about co2 laser cutter types and prices
Post time: Sep-20-2022